How IoT Monitoring Is Revolutionizing Cold Chain Logistics
In today’s fast-moving supply chains, especially those handling perishable goods, cold chain monitoring has become more than just a regulatory requirement, it is a competitive advantage. Thanks to IoT (Internet of Things) technology, businesses now have the power to track and protect temperature-sensitive products with greater accuracy, automation, and real-time insights.
What Is Cold Chain Monitoring?
Cold chain monitoring refers to the process of tracking temperature and environmental conditions throughout the storage and transportation of perishable goods such as vaccines, seafood, frozen food, or chemicals. The goal is to ensure products remain within specific temperature ranges to avoid spoilage, loss, or non-compliance.
Traditionally, cold chain monitoring relied on manual checks or basic data loggers. These methods often left blind spots and delays in detecting problems could result in damaged inventory.
Enter IoT: A Smarter Way to Monitor the Cold Chain
IoT monitoring brings automation, real-time visibility, and intelligent alerts into cold chain operations. Here’s how:
1. Real-Time Temperature and Humidity Tracking
With IoT sensors installed in cold rooms, reefers, or transport boxes, businesses can continuously monitor conditions 24/7. Unlike manual systems, these sensors send live data to a central platform, allowing teams to see exactly what’s happening — as it happens.
2. Instant Alerts for Faster Response
If a temperature deviation occurs — for example, a freezer door left ajar or a reefer unit malfunction — the system triggers real-time alerts via SMS, email, or app notifications. This gives your team a chance to act immediately, reducing losses and protecting product quality.
3. Cloud-Based Dashboards and Reports
IoT monitoring platforms store data in the cloud, offering historical insights, trend analysis, and compliance-ready reports. This helps businesses not only stay audit-ready but also identify recurring problems and improve operations over time.
Cold Chain Monitoring in Transit: From Warehouse to Delivery
One of the most impactful uses of IoT is in mobile cold chain monitoring — tracking goods as they move through the supply chain.
In case of route delays or unexpected temperature spikes, fleet managers can be alerted immediately and take corrective action.
GPS integration allows businesses to track the location and condition of products in transit.
Battery-powered IoT devices ensure continuous monitoring, even when cargo is on the road or in remote locations.
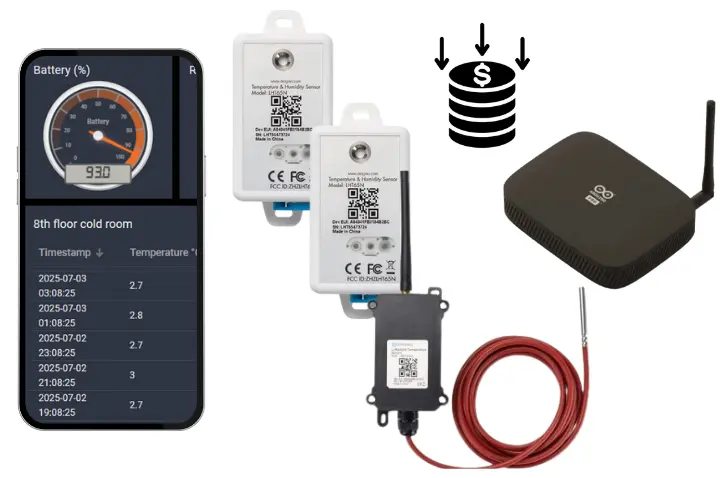
Real-World Impact: Pharma and Food Safety
In the pharmaceutical industry, where vaccines and biologics must stay within narrow temperature ranges, IoT cold chain monitoring ensures regulatory compliance (e.g. WHO, FDA, GDP) and patient safety.
In food logistics, real-time monitoring helps companies meet HACCP standards, reduce spoilage, and protect brand reputation — especially during hot weather or long-distance shipping.
Key Benefits of IoT Cold Chain Monitoring
- ✔️ Reduced product spoilage and waste
- ✔️ Faster response to temperature excursions
- ✔️ Improved compliance with regulations
- ✔️ Better visibility across multiple locations and vehicles
- ✔️ Data-driven decision-making and optimization
Shop Now at IOT-ezy
Protect Your Assets and Start Monitoring